Custom Injection Molding Services in Illinois
Needing custom plastic molding in Illinois and the Midwest region is not uncommon today. There are times when a part must fix exactly with another part or a part might have intricate parts. For example, a medical part or military component may have a complex design. All the components in these types of applications must meet strict compliance requirements and strict specifications. The complexity of a project may also dictate the need for custom plastic injection molding. Custom plastic injection molding relies on process technologies, analytical tools and numerous scientific methods. True custom injection molding companies in Illinois use the four stages of product development: scientific molding, insert molding, multi-shot molding and over molding.

Scientific Molding
Scientific molding relies on precise measurement and material science. All of the data is recorded during the process, so multiple production runs can be operated. Highly-trained engineers use scientific molding data and recognize small changes in flow rate, temperature and pressure. Often, these specialists are highly knowledgeable in a specific phase of product development. They have to know all about material chemistry, fill time and mold conductivity. With their expertise, a product can be designed and made to meet high quality requirements and to be defect-free. When it comes to scientific custom molded plastics and plastic mold components, a knowledgeable engineer is needed.
Custom Insert Molding
Insert molding is a technique used by many custom injection molding companies in the manufacture of precision molded plastics. A solid component is placed into a tool, and resin is injected into the cavity. The insert can be a combination of single components that are sealed together during the process. The benefits of insert molding for custom plastic parts manufactures included cost saving, stronger parts and consistency. When performing insert molding, it is critical to have highly-controlled processes and controls in place to maximize quality.
Custom Over Molding
Over molding is a custom plastic molding process that’s sued for military equipment, hospital equipment, power tools, smartphones and tablets. All of these devices have something in common. They are made from plastic. With over molding, the molded plastic form provides strength, a precise looking shape and sometimes bright colors. They are pleasant to the tough and don’t slip. Over molding involves molding an outside layer around an inner structure. It’s a two-stage process, and the end result is high resilience. It’s also an option for highly intricate pieces that are too hard to made with just one injection process. Over molding requires experience and skill. Care is needed at every step of the design and production process.
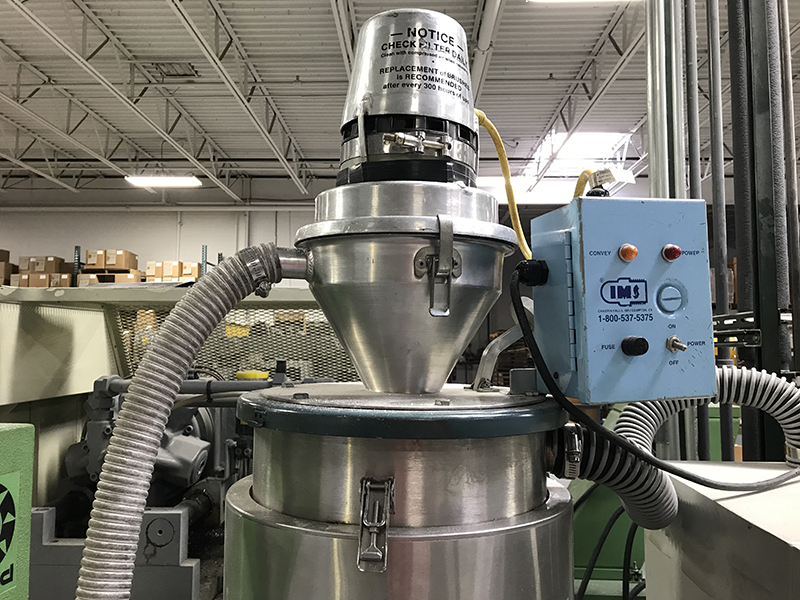
The Advantages of Custom Plastic Molding
Custom injection molding offers many advantages. “Its broad flexibility design affords the ability to design highly complex pieces according to the needs of the customer. While there are a number of best practices for injection molding that help to ensure efficient production and suitable part quality and reliability, the possibilities within these design best practices are quite broad. Its advanced processes, such as co-molding and over molding make injection molding a simple way to add even more customization to your part or product. In a nutshell, utilizing a process such as over molding means that your injection molded part doesn’t need to be limited to materials suitable for injection molding. Widely variable tooling costs is another benefit. Often, the cost of the mold or tool is cited as a barrier to entry for many customers who may wish to have a part injection molded, but don’t want to (or aren’t able to) meet the high cost of production for high-quality tool steel molds. There are a number of other options available for tooling — including, as mentioned above, 3D printed molds, which can offer the quality needed for prototyping or low-quantity production runs. In addition, other, “softer” metals such as aluminum molds can be very effective for short-to-medium productions runs — reliably producing quality parts in quantities up to the thousands (or more). Be sure to work with a supplier that’s willing to discuss your needs, and help you meet them.”
Another advantage is fast turnaround time compared to other process. This makes it more cost-effective. A good custom molding company will allow you to work with different types of quantity, including prototype runs, low run and large runs. The options for control are many. All around, custom injection molding is viable, cost-effective, high quality and quick.
Crestwood- One of the Highly Sought After Custom Injection Molding Companies
Custom plastic injection | Custom molded plastics | Plastic mold components
Crestwood is one of the highly sought after custom plastic parts manufacturers. Its capabilities, areas of expertise and certifications may it a very successful company. Crestwood offers:
- Collaborative engineering and product development support
- Products for critical use
- In-house tooling design, engineering and management
- Product development control utilizing scientific molding
- Secondary operations
- Two-shot, insert molding and over molding
- State-of-the art quality control equipment
- Vertical and horizontal presses
- Industry certifications
- Metal-to-plastic applications and conversions
- Custom plastic injection, custom molded plastics and plastic mold components
If you’re in need of a high quality product, turn to the experts in custom plastic molding at Crestwood. The hallmarks of Crestwood are high quality, trained engineers, experience and excellent customer service. You’ll be supported even after your project is completed.Crestwood has experience in a wide variety of industries, including medical, military and retail. Fill out their form, call or text them today. Even call to have your questions answered and receive a quote.