Crestwood Industries – Top / Low Volume / Custom Injection Molding Company
Injection molding services is a manufacturing method for making objects by shooting molten material into a mold. Material is fed into a barrel and then led into the mold. It then cools and takes on the shape of the mold. Typically, the part is aluminum, steel or plastic. Precision plastic injection molding manufacturer is done for automotive parts, medical devices, mechanical parts, toys, chairs, musical instruments and more. It is also used for low volume injection molding parts and engineered plastic components. Prototype injection molding is ideal for producing a high volume of the same object. This process is preferred by many businesses.
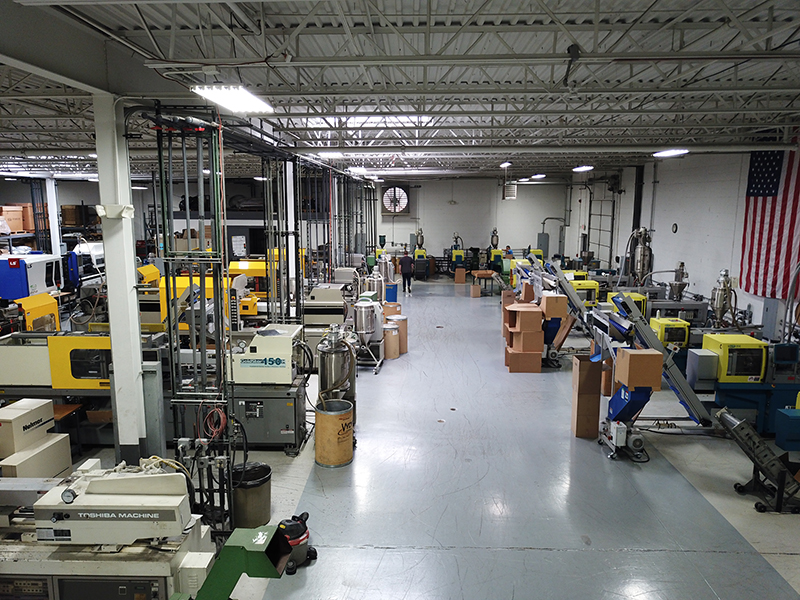
The Injection Molding Press-How It’s Done
When thermoplastics are molded, the raw material is fed into a heated barrel with a screw. The screw delivers the raw material, and the temperature is increased. The material is then fed through a check valve and collects into a volume called a shot. This is what is used to fill the mold cavity. When there is enough material, the material is forced at high pressure. Injection times are less than one second. The material then hardens during a cooling period by circulating water. For thermosets, two different materials are added to produce parts with several performance characteristics. A chemical reaction occurs and results in a shorter time to solidify the parts. Insert molding allows single parts to have multiple materials and is usually used to create plastic parts that have metal screws.
The Many Benefits of Plastic Molding Manufacturing-From Operations to Costs
There are many benefits of plastic molding manufacturing.
- Quick Turnaround: Top quality parts can usually be completed in just 10 days. Time is money.
- Efficiency: In high volumes, there is more efficiency, as less water is used during this process. In addition, less supervision is required due to the automated equipment used in the process.
- Scalability: Custom production from 250-25,000+ parts can be done. Smaller orders can be scaled into larger ones when needed.
- Precision: Molds are machined to exact precision. There is a careful selection of resins and chemical compatibility. Thousands of parts can be reproduced with intricate and small details. Get the exact details needed.
- Cost Effective: Plastic molding manufacturing is much less in cost than other processes.
- Strength: Molded parts perform better since they are made using compatible materials. This adds strength to the product produced.
- Options: Injection molding capabilities include unlimited undercuts, internal or external threads, insert molding, custom colors and over molding. Like-life parts can be created.
- Needs Met: Businesses can find prototype injection molding for smaller part quantities and on-demand manufacturing tool for large part quantities. This includes engineered plastic components and low volume injection molding.
Compared to the costs of other processes of molding manufacturing, plastic custom injection molding is considerably less. The bottom line is that this process can put out more parts faster, resulting in less time required for the production and realization of your plastic parts and products. Automatic equipment is also used throughout to streamline the process and make it more efficient, meaning fewer workers are required and there is a drastically lower margin for human error. Automation allows us to pass those savings on to you while retaining a smaller, more specialized workforce.
Plastic injection molding services can also provide a much higher level of complexity when required in your projects. This is because injection molds are regularly subjected to high pressures, resulting in the plastic materials within the molds to be pressed harder against the mold when compared with other processes. The high pressure enables the easy production of highly complex and intricate shapes which would be too expensive and complicated to achieve with other manufacturing methods.
Our Plastic Injection Molding Services Are More Environmentally Friendly Than Other Manufacturing Methods
We are committed to providing quality products in a sustainable way that is safe for the environment. Crestwood Industries strives to cut down on the excess plastic that is typically generated during high and low-volume injection molding processes.
This includes our use of nontoxic materials when available. In our injection molding facilities, we aim to use colorants, cleaners, lubricants, and resins that are non hazardous and nontoxic. They are better for our workers, your business, your customers, and the environment.
We also seek to recycle when we can, meaning that by choosing Crestwood Industries, you aren’t only getting the absolute best when it comes to exemplary customer service and high-quality manufacturing, but you are also supporting green initiatives that will ultimately lead to a better, cleaner tomorrow.
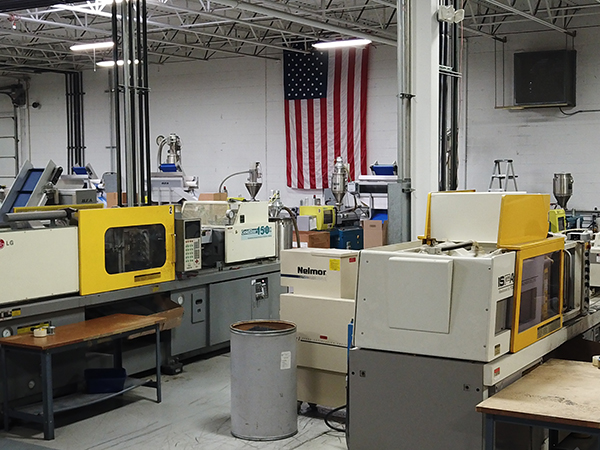
Prototyping vs On-Demand Manufacturing Tool-Which is Better?
Prototyping is good when you need design feedback. You can get interactive design feedback before prototyping even begins. Plus, you can quickly modify designs before actual product development. This can save money before investing. Multiple prototypes can even be produced. Prototyping lessens the overall time to market. In addition, you get design validation. Functional tests can be performed on small quantities of molded parts. This reduces financial risk. Prototyping is also a good fit when you want to run a pilot launch before a final one. Test it out before bringing it to market.
On-demand manufacturing works well for low-volume runs. It’s easy to manage inventory overheads and can be the primary production method for a few thousand units. On-demand manufacturing also minimizes the risk of stock-outs and increases demand volatility. You can procure parts on demand and benefit from less inventory costs and warehousing expenses.
All About Crestwood Industries
Crestwood Industries – a top injection molding company in Illinois – offers full in-house plastic molding services from prototyping to large scale projects. They use state-of-the-art molding machines that deliver high quality. Crestwood Industries offers:
- Specific shot sizes
- A variety of pressies
- Advanced software to maximize quality
- High precision parts from both high temperatures to low temperatures
- Intricate multi-cavity tooling
- Medium and Small parts from engineering-grade resins
- High tolerances
- Assembly, testing, milling, sonic welding, tapping and drilling
Years of experience have made Crestwood Industries a leader in the industry of plastic injection molding manufacturers. In addition, Crestwood Industries has a team that can also custom design a mold, conduct process development for accuracy, offer preventative maintenance and do both minor and major repairs.
The presses at Crestwood Industries are managed by expert staff and experienced workers. Every machine is equipped with a robot. Parts are counted and boxed as they come off the conveyor. Each press is self-diagnostic and microprocessor-controlled. Quality control is a priority at every step of the process. Parts are inspected using a high-tech system. Quality control checks are also performed as the products are sorted, weighed and sealed. From the beginning to end, the whole process is monitored for quality.
The team at Crestwood Industries will work closely with you to help determine the right materials and colors. They will find out whether your product needs to be fire retardant or have special coloring. All around, you can trust Crestwood Industries – custom injection molding company to deliver a quality product that not only meets your needs but surpasses it. This is one of the many reasons why Crestwood Industries is most sought after in the industry. When businesses need quality, intricate parts at a competitive price, they turn to Crestwood Industries. If you need high-quality parts manufactured, turn to the experts at Crestwood Industries. Fill out their form for contact, text or call them. They are always more than happy to answer any of your questions and to provide you with a quote. Turn to Crestwood Industries for their plastic injection molding service.
Low Volume Injection Molding
A great number of businesses and companies require low volume injection molding to fulfill the needs of much more demanding customers in modern days. Customer expectations are rising every year and going for low volume production allows business owners to experiment with new product concepts and markets with much less risk.
Low volume injection molding is still one of the best ways to do this, even with the rise of 3D printing methods. This is primarily to do with the prohibitive cost and expertise required to be able to produce affordable, low-cost plastic parts. It is set to remain king in the foreseeable future for producing prototypes and custom large parts through our prototype injection molding and large part injection molding services.
Depending on the overall design and complexity of the plastic part required, an injection mold needs to be customized and created to achieve the right standards, working tolerances, finish, and specifications so that it is functional to the purpose of the design. These parts of the process are crucial. We ensure that each client is involved in each step of the production to ensure that we are fulfilling your needs and expectations.
Low volume injection molding is the perfect method for shortening lead times to give you quicker production turnarounds and, more importantly, can provide versatility concerning your budget. Once you have approved or are happy with the production, you can also have the option of scaling the low volume production up to mass production, dependent on your requirements.